The Sand Casting Process
Even a child playing at the beach or in a sandbox can immediately grasp how sand casting works. When you see a child mixing water into sand to make it easier to shape it into a sand castle, that child is demonstrating how combining some sand and water works so beautifully for creating a shape.
At its simplest, the sand casting process for a casting foundry is nothing more than making a cavity in the sand in the desired shape, pouring molten metal into the cavity and letting it cool. Humankind has been doing this for thousands of years. Sand is heat resistant and readily available almost anywhere on earth.
If you’ve ever noticed the way footprints made in wet sand hold their shape, you can easily imagine what likely inspired the first ancient metal workers to use wet sand to shape their cast metals. Everything after that has just refined and perfected the basic process.
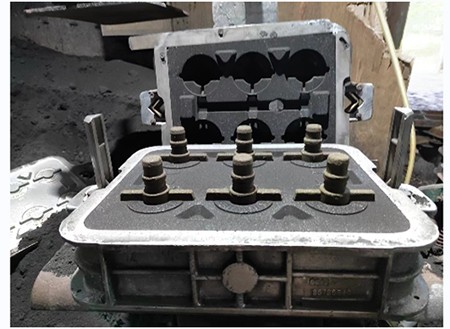
What Is Green Sand Casting?
The term green sand has nothing to do with the color of the sand casting material. It means there’s some moisture in the sand; when the sand is said to be green, it means the mold has not been baked or dried. This kind of molding sand is a very economical and versatile material. When desired, the foundry can add select additives can make the green sand more ideal for a specific purpose. Green sand is used in the most common sand casting processes.
How Do You Make Sand Casting Molds?
Sand casting equipment within a foundry can be very basic or quite advanced, depending on the items being made. Typically, the sand is placed in a mold box, which is known as a flask. The pattern, or model, is placed in the prepared sand inside the flask to make a mold. The pattern is removed, leaving behind a perfect shape in the sand. The mold is filled with molten metal, which is allowed to cool. When the metal is sufficiently cooled, the sand mold can be broken away.
More complicated items can be cast by combining an upper and a lower section. The upper mold is known as the cope, while the bottom half is known as the drag. Once the cope and drag are ready, they can be fastened together so that molten metal can be poured into the resulting cavity. Even further detailing is possible with the addition of a core. A core is something placed inside the mold to form a negative space that no molten metal will fill. An example would be the middle of an engine block or any other cast item that requires a hollow space.
Castings made with cope and drag must provide a way to introduce the molten metal into the mold. It can be a simple vertical passage, known as a sprue. The sprue and its channel will fill with molten metal that will solidify and will need to be machined off to get the item to its final design.
How Does The Sand Casting Process Work?
In the modern foundry or casting industry, the knowledge of how each alloy will react with each potential form of mold and each potential additive allows the worker to make choices to give the finished item the desired characteristics. Metal casting is both an art and a science.
As the molten metal cools and solidifies, it will give off gasses. The molds are designed to take that into consideration and when necessary, will be constructed to allow the gasses to escape throughout the sand casting process.
What Is Sand Casting Used For?
Chances are good that you’re less than 10 feet from at least one cast item right now that has been through the sand casting process. There’s hardly an industry that doesn’t have some kind of need for cast materials. Some cast items are large and can weigh hundreds of pounds, while other cast items are tiny and intricate.
What Are Some Common Metals Used in Sand Casting?
Almost any kind of metal can be shaped using the right sand casting equipment. Grey iron and ductile iron very well.
What Additives Are Common In Sand Casting?
Modern manufacturers will usually add some water and other additives to the sand casting process to make it work better for various purposes. Different alloys and different items call for additives, including these common materials:
-
- Clay: It could be bentonite clay (most likely calcium bentonite) or another kind of clay. For special delicate and high-detail items, such as jewelry, Delft clay, which is imported from the Netherlands, can be used.
- Coal Dust: Also known as Sea Coal, this is added to produce a more even surface, to make it easier to get the cast item out of the mold. It also produces casts with fewer defects.
- Corn Flour: Believe it or not, a little bit of corn flour added to the wet sand gives the sand greater strength and plasticity.
- Dextrin: Dextrin, derived from corn starch, is used as a binder. It improves the dry surface strength of the sand.
- Pitch: Made from soft coal, a little pitch added to the sand improves the surface finish.
- Wood Flour: This material is combustible, which like other combustible additives helps create a space for the grains of sand to expand without changing the shape of the mold.
- Silica Flour: This material is just finely ground sand that’s mixed into casting materials for a more durable mold.
What’s The Future In Sand Casting?
Relatively new technology in today’s casting foundry is 3D printed patterns and molds.
The latest 3D printing equipment is capable of manufacturing a sand mold and core in just a few hours. This can save considerable time and money in some cases.
Once the pattern is produced, sand casting proceeds as usual, but the ability to use a 3D printer to produce the pattern, molds and cores greatly speed up the process, potentially saving production costs and increasing the accuracy of the casting. If an example of the item to be sand cast already exists, it can easily be scanned to create the 3D model.
Once the program for producing the sand mold and core is perfected, it can be reproduced as many times as desired. Such sand casting equipment is a growing part of the metal casting industry. The sand casting advances of today would no doubt amaze the master sand casters from a hundred years ago — not to mention those of a thousand years ago!
Why Do Some Cast Items Require Machining?
In some cases, an item produced through the sand casting process requires machining, painting, or another process to bring it to completion. Oftentimes, the item will have extraneous material necessary to make a good cast but not meant to be part of the finished design. At other times, fine detailing is needed and can be added after the cast is completed. Cast Technologies has a CNC machine shop on-site in order to deliver a finished product that meets your needs. This allows us to serve our customers better, as we take responsibility for all the processes the part requires to meet its design specifications.