The metal casting process can create anything from tiny fasteners to large industrial components, all through a five-step procedure. It happens by creating a pattern and making a mold, melting and transferring the metal and finishing, cleaning, polish and inspecting the casting. While metal casting is a straightforward practice, it requires specialized skills and techniques to perfect.
At Hengchang Foundry, we have the mastery and technology to form objects of various sizes for different industries like heavy equipment and transportation. No matter the complexity of the parts you require, our professional team can produce tailored castings to deliver unique parts for your application.
What is the metal casting process? Continue reading to learn what to know about metal casting and how our metal casting services work.
1. MAKING THE PATTERN
When talking about a pattern, we aren’t referencing one you trace on a piece of paper. Instead, metal casting foundries refer to patterns as a replica of the object they’re casting. This pattern helps form the mold cavity, which can be made of wood, plastic, aluminum and many other suitable materials. Making a pattern is a crucial first step because the accuracy of the mold determines the accuracy of the final product.
The four steps in producing a precise pattern include:
- Shaping the mold cavity
- Adapting the properties of the metal cast
- Referencing accurate dimensions
- Creating a way for the liquid metal to enter the mold
Depending on the type of material being poured into each mold, the final, solid product will distort to a certain degree. For example, it may shrink compared to the original size of the mold. This is why each pattern has allowances for slight alterations. Additionally, patterns require a draft, or a vertical tapered wall, where professionals can extract the pattern without tampering with the molded product.
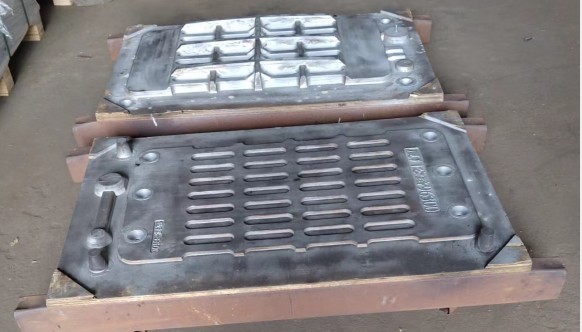
2. CREATING THE MOLD
It’s now time to create the mold, which is a hollow shape that will form the metal later on in the process. While some molds are expendable, others are nonexpendable.
An expendable mold means you can’t use it again. In that case, materials like sand, plaster foam or plastic make up the mold, and they’re destroyed during the casting process. Alternatively, you can use nonexpendable molds indefinitely, as they’re often made of aluminium.
Both expendable and nonexpendable molds can support different pattern complexities and materials.
3. MELTING AND TRANSFERING THE METAL
While we use a multitude of materials for metal casting, they all fall under one of two categories — ferrous and non-ferrous metals. The metals used in metal casting can include iron, zinc, aluminum, tin, copper, lead alloys and others. While a ferrous metal contains malleable iron or steel, a non-ferrous metal contains nonmalleable metal, such as copper, nickel or aluminum.
After selecting the appropriate metal type, we load it into the furnace where temperatures rise until it reaches the material’s melting point. At Warner Brothers Foundry Company, we use gas furnaces during the metal casting process, though there are two other common types of furnaces for metal casting — electric arc and induction.
Using electric furnaces is our preferred method for metal casting because it burns cleanly and efficiently. Electric furnaces also allow us to heat the metal to the necessary temperatures without using high amounts of electricity. Electric furnaces are more efficient for our process, which keeps costs lower on our end and allows us to offer lower prices on your end.
Once the material melts down, it’s transferred to a large ladle before it reaches the mold. Through gates and risers, or openings in the mold, workers or machines pour the liquid material into the mold. Once it takes shape, solidifies and cools, we eject the casting from the mold, removing excess metal from the gate and rider system before moving to the next step in the process.
Understanding how long metal casting takes depends on the material — some may cool within minutes, and others take several days.
4. FINISHING AND CLEANING EACH PART
This stage involves making the final touches and cleaning each individual part. At Hengchang Foundry Company, we go in and remove excess metal parts and begin the cleaning process, using different tools to clear away particles and dirt. The final product is the same proportion and shape as the original pattern used during step one.
Additionally, some products may require a heat treatment, such as rail clamp, hydraulic cylinder, buffer. This process alters the properties of the material through a heating and cooling technique where the metal becomes more resilient. These treatments are ideal for applications that may endure extreme weight, wet environments or freezing temperatures.
5. INSPECTING THE CASTING
The metal casting process ends with an inspection to ensure everything is complete and up to our standards. During the final stage, we check the part’s physical structure and integrity to ensure it’ll hold up and perform the expected job.
There are destructive and nondestructive testing methods, which are put in place depending on the casting’s specifications. In particular, visual inspections include looking for cracks, accuracy and surface finishes, and more in-depth testing checks tensile strength, hardness and ductility, among other components.
No matter the industry, we inspect everything from trailer hitches and industrial equipment to small automotive parts. In the end, you’ll have a durable component that’s suited to your unique needs and operations.